
can obtain statistics on performance and degradation of installed insulator assets.is safe to operate on energized lines using an isolating hot-stick or drone.does not rely on judgement of testing personnel to identify defects.has high sensitivity to detect even small defects (including floating defects) before they produce detectable IR or UV radiation.does not depend on climatic conditions or is affected by angle of view.includes automatic counting of the insulator’s sheds or bells and records measurements and their locations in a quantifiable database.
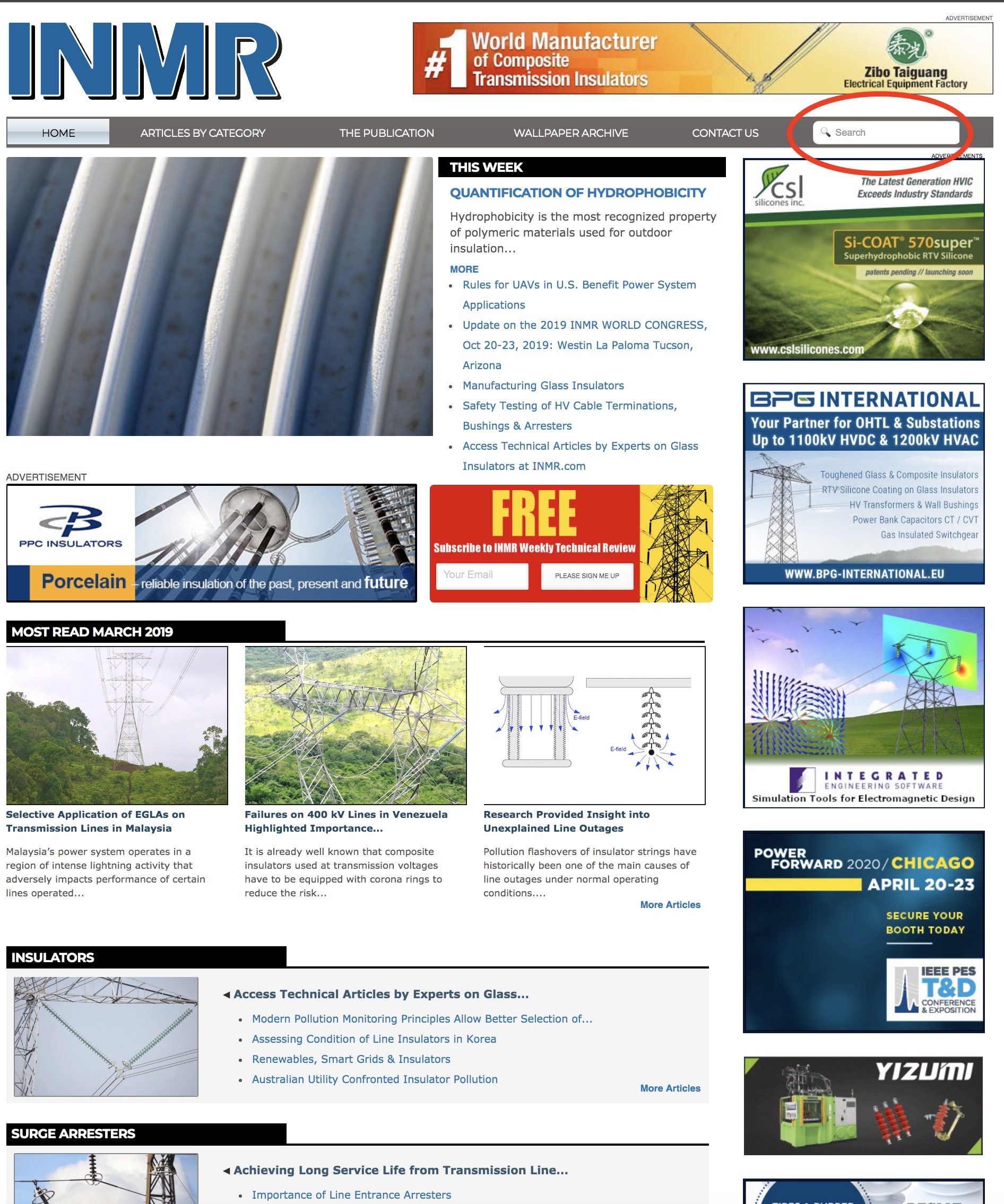
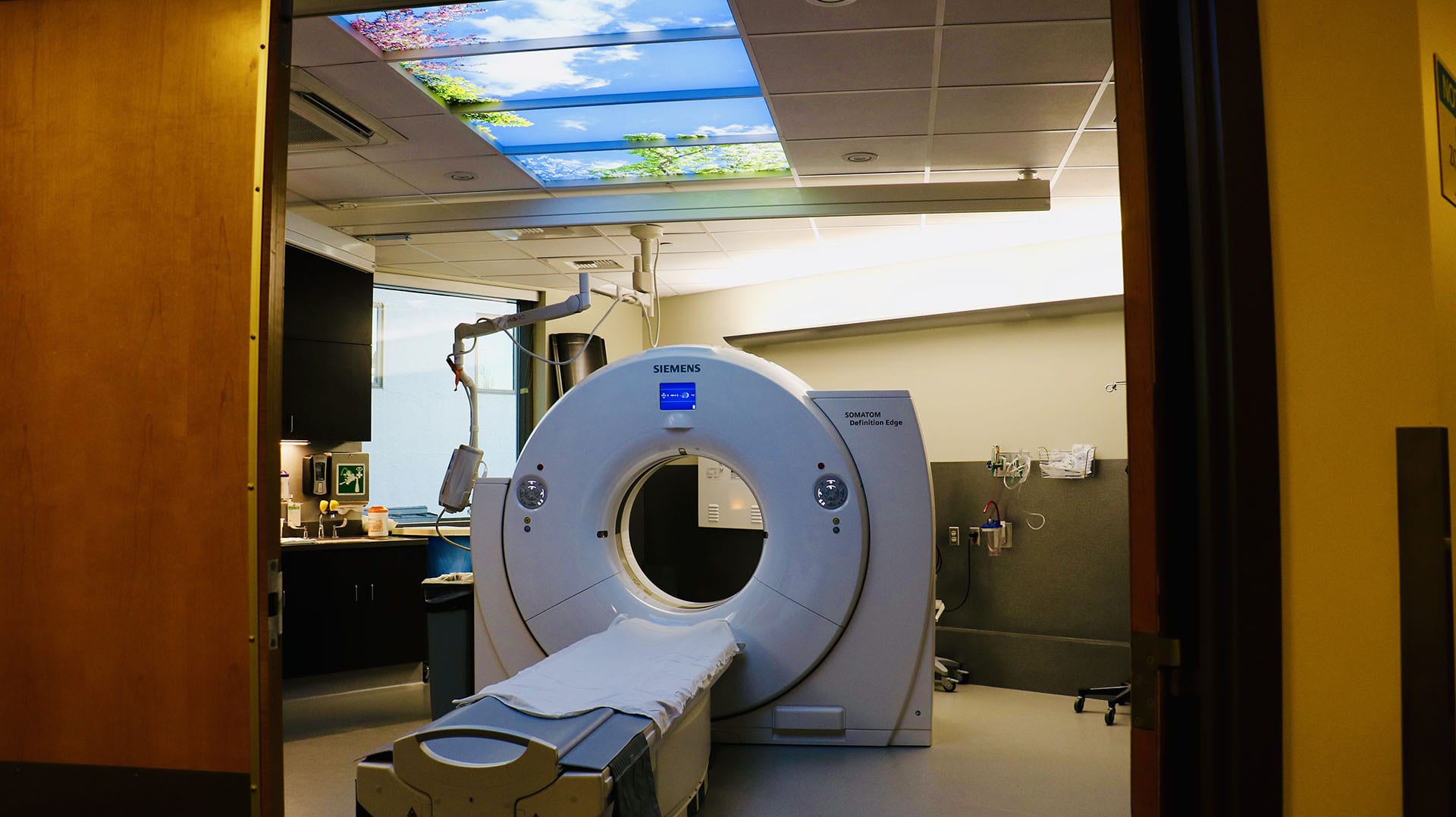
This enables detection of the size of the defect, provided the sensor module is sufficiently sensitive. Moreover, length of that distortion is directly proportional to size. Any conductive defect, internal or external, causes distortion in the strength of that E-field in the immediate vicinity of the defect.

Potential difference gradient along an energized insulator creates an electric field (E-field) that surrounds the insulator in concentric circles. An overview is also presented of some of the most common problems encountered on porcelain and composite line insulators, including moisture ingress, carbon tracking, surface contamination and manufacturing defects. Charles Jean of Positron Power in Canada reviews how this methodology evolved and claims it can prove effective in detecting even small defects that might not always be identified using other inspection methodologies. The methodology utilizes measurement of E-field distribution along insulators to detect presence of any conductive defects as well as record and display their severity and location. Early detection of defective insulators avoids risk of significant problems and enables scheduled maintenance as well as maximum safety prior to live-line work. The electric field method has been used for over 30 years to test and verify the condition of energized porcelain and composite insulators on overhead transmission lines.
